Detailed process model description for the Pasteurization demo
Model specification
Introduction
Intended audience
The present document is oriented to:
-
Model developers
-
Model users
-
System Integrators.
Scope
The scope of the present document is to describe the capabilities of the Pasteurization demo, for the process modeling of continuous (i.e. flash) pasteurization processes.
Prerequisites
-
basic knowledge of process engineering and / or of food processing.
-
know about the different roles involved with the lifecycle of solutions developed using the LIBPF® enabling technology, see LIBPF® Technology Introduction
Pasteurization kernel
In LIBPF® one kernel can support many process models, each as a different flowsheet type.
All the process models supported by a kernel share the same list of components and can use all LIBPF® embedded types plus the custom types registered by the kernel itself.
Type list
The Pasteurization kernel registers the following process models, based on the built-in LIBPF® FlowSheet type:
Type | Name | Description | options | Note |
---|---|---|---|---|
Pasteur | Pasteur | Configurable pasteurization process | processType=“user” feedType=“user” | default model type |
Pasteur | PasteurHTST15_milkWhole | High Temperature Short Time Pasteurization 15 s of whole milk | processType=“HTST15” feedType=“milkWhole” | alias of the default model type |
Component list
The fluids to be processed are broken down in their constituents and represented as a mixture of basic food components.
The components are defined using built-in LIBPF® basic types.
More precisely the Pasteurization kernel defines the following component list (click on the component type to jump to the reference documentation for the component):
Type | Name | Description |
---|---|---|
purecomps::water | water | standard model for water |
purecomps::Protein | prote | ChoiOkos organic protein component |
purecomps::Lipid | lipid | ChoiOkos organic lipid component |
purecomps::Carbohydrate | carbo | ChoiOkos organic carbohydrates component |
purecomps::Fiber | fiber | ChoiOkos organic fiber component |
Process description and scheme
The pasteurization process is designed to reduce the bacterial load of edible fluids such as milk, milk products, beer, wine, fruit and vegetable juices, ice cream mix etc..
The continuous (i.e. flash) pasteurization actually consists in keeping the fluid at a defined hot temperature for a defined short time. Temperature and time must be carefully balanced to prevent the thermal wear of the food and, at the same time, to kill as much as possible pathogenic microbes.
For this purpose, the fluid must be pumped, quickly heated to the desired temperature and held to that temperature using a pipe of proper length. After that the fluid must be quickly cooled at a temperature which can be suitable for storage. It is possible to recover part of the heat by pre-heating of the inlet fluid using the hot treated fluid.
The following process flow diagram should clarify the process.
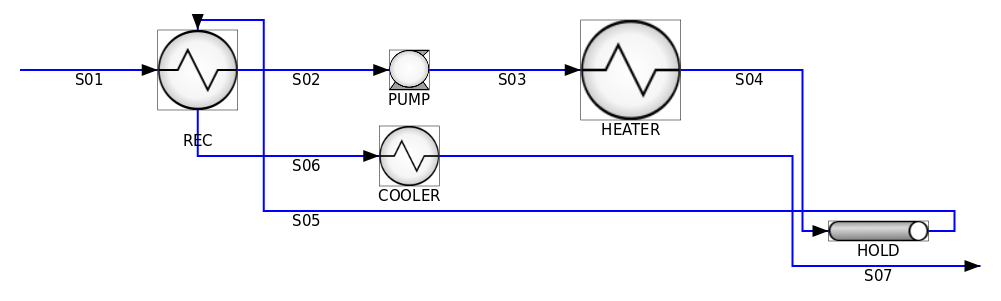
The cold fluid to be processed (S01) enters the cold side of the REC recuperator heat exchanger, where it recovers energy from the hot pasteurized fluid S05.
The pre-heated fluid S02 is pumped via PUMP through the HEATER heat exchanger, which rapidly brings it to the required temperature. The resulting hot fluid S04 is held at this temperature for the required time in a long pipe HOLD.
The hot pasteurized fluid S05 recovers heat with the cold feed in the hot side of the REC recuperator heat exchanger.
The warm fluid S06 is rapidly cooled at the storage temperature in the COOLER heat exchanger.
Stream list
The streams are defined using built-in LIBPF® basic types.
Click on the type to jump to the reference documentation for the stream.
Type | Name | Description | From | To | options |
---|---|---|---|---|---|
StreamLiquid | S01 | Fluid inlet | source out | REC coldin | |
StreamLiquid | S02 | Pre-heated fluid | REC coldout | PUMP in | |
StreamLiquid | S03 | Pumped pre-heated fluid | PUMP out | HEATER in | |
StreamLiquid | S04 | Holding hot fluid | HEATER out | HOLD in | |
StreamLiquid | S05 | Pasteurized fluid | HOLD out | REC hotin | |
StreamLiquid | S06 | Warm fluid | REC hotout | COOLER in | |
StreamLiquid | S07 | Cooled fluid outlet | COOLER out | sink in |
Unit list
The unit operations are defined using built-in LIBPF® basic types.
Click on the type to jump to the reference documentation for the unit operation.
Type | Name | Description | options |
---|---|---|---|
Exchanger | REC | Recuperator | |
Pump | PUMP | Liquid circulation pump | |
FlashDrum | HEATER | Pasteurization heater | |
Pipe | HOLD | Holding pipe | |
FlashDrum | COOLER | Cooler |
Model options
Continuous pasteurization processes may be operated with different combinations of hot temperature and holding time.
These condition are usully defined by technical regulations.
For this reason the model can get an input string option (processType) which adjusts temperature and holding time.
The feedType string option is available to choose a predefined composition for the fluid to be processed.
processType option
The process type option sets predefined temperature and holding time for the process.
option | description | effect |
---|---|---|
HTST25 | High Temperature Short Time | highT = 353.15 K holdTime = 25.0 s |
HTST15 | High Temperature Short Time | highT = 356.15 K holdTime = 15.0 s |
HHST3 | Higher Heat Shorter Time | highT = 363.15 K holdTime = 3.0 s |
HHST1 | Higher Heat Shorter Time | highT = 363.15 K holdTime = 1.0 s |
user | default: highT = 363.15 K holdTime=1.0 s | let the user to adjust the temperature and time as usual input parameters |
feedType option
The feed type option sets the composition of the fluid to be processed to certain predefined values.
option | description | effect |
---|---|---|
milkWhole | Milk, whole, 3.25% milkfat, with added vitamin D | water = 0.8813 prote = 0.0315 lipid = 0.0325 carbo = 0.0480 fiber = 0.0 |
chocolateIceCream | Ice cream, soft serve, chocolate | water = 0.598 prote = 0.041 lipid = 0.130 carbo = 0.222 fiber = 0.007 |
eggWhole | Egg, whole, raw, fresh | water = 0.7615 prote = 0.1256 lipid = 0.0951 carbo = 0.072 fiber = 0.0 |
vanillaFatFreeIceCream | Ice creams, BREYERS, 98% Fat Free Vanilla | water = 0.6342 prote = 0.0330 lipid = 0.0220 carbo = 0.3051 fiber = 0.054 |
user | default: water = 1.0 prote = 0.0 lipid = 0.0 carbo = 0.0 fiber = 0.0 | (default) user specified - initial composition set to pure water, user adjustable (S01:Tphase.x[i] with i representing the component index or component name) |
Model parameters
Inputs
At the top-level of the flowsheet object hierarchy there are the following input parameters:
-
coolT: Cooling temperature for the storage of the pasteurized fluid
-
highT: Hot temperature for pasteurization (Available only if processType is “user”)
-
holdTime: Time to keep fluid to designed hot temperature (Available only if processType is “user”)
-
dTexchangeLL: Delta T approach for liq-liq exchanger (used to specify the REC cold side temperature increase);
-
feed: Feedstock fluid mass flow
-
press: Fluid outlet relative pressure
-
hs: Design speed in the holding pipe (used to calculate the pipe diameter)
There are also available other input variables inside the unit operations and streams:
Tag | Value | Units | Description |
---|---|---|---|
coolT | 278.15 | K | Cooling temperature |
dTexchangeLL | 20 | K | Delta T approach for liq-liq exchanger |
feed | 1 | kg/s | Feedstock fluid mass flow |
highT | 363.15 | K | Heating temperature |
holdTime | 0.000277778 | h | Time to keep fluid to designed temperature |
press | 1e+06 | Pa | Fluid outlet relative pressure |
COOLER.deltaP | 20,000 | Pa | Pressure drop |
HEATER.deltaP | 10,000 | Pa | Pressure drop |
HOLD.eps | 4.57e-05 | m | Rugosity |
HOLD.h | 0 | m | Elevation positive for ascending |
HOLD.s | 0.005 | m | thickness |
HOLD.vhConcentrated | 0 | velocity heads due to concentrated pressure losses | |
PUMP.V | 380 | V | Voltage |
PUMP.cosphi | 0.9 | cosine of phi | |
PUMP.duty | 0 | W | Duty inlet - outlet |
PUMP.etaE | 0.9 | Electrical efficiency | |
PUMP.etaM | 0.9 | Mechanical efficiency | |
REC.U | 1,278 | W/(m2*K) | Overall heat transfer coefficient in terms of dutyhot |
REC.deltaPcold | 10,000 | Pa | Pressure difference for cold stream |
REC.deltaPhot | 10,000 | Pa | Pressure difference for hot stream |
S01.P | 101,325 | Pa | Pressure |
S01.T | 277.15 | K | Temperature |
S01:Tphase.x[0] | 1 | Mole fraction water | |
S01:Tphase.x[1] | 0 | Mole fraction prote | |
S01:Tphase.x[2] | 0 | Mole fraction lipid | |
S01:Tphase.x[3] | 0 | Mole fraction carbo | |
S01:Tphase.x[4] | 0 | Mole fraction fiber |
Results
At the top-level of the flowsheet object hierarchy there are the following results:
-
Qin: Thermal power input (duty of the HEATER)
-
Qout: Thermal power output (duty of the COOLER)
-
Win: Work power input (PUMP electrical consumption)
-
Acooler: Cooler exchange surface
-
Aheater: Heater exchange surface
-
Arecuperator: Recuperator exchange surface
-
highT: Hot temperature for pasteurization (Available as output if processType is not “user”)
-
holdTime: Time to keep fluid to designed hot temperature (Available as output if processType is not “user”)
There are also available other results inside the unit operations and streams:
Tag | Value | Units | Description |
---|---|---|---|
Acooler | 10,11 | m^2 | Cooler exchange surface |
Aheater | 10,28 | m^2 | Heater exchange surface |
Arecuperator | 1,03 | m^2 | Recuperator exchange surface |
Qin | 262747,8 | m^2 kg s^-3 | Thermal power input |
Qout | 258413,05 | m^2 kg s^-3 | Thermal power output |
Win | 1299,08 | m^2 kg s^-3 | Work power input |
cduty | 1 | m^2 kg s^-3 | Cumulative enthalpy flow inlet minus outlet |
cmdot | 1 | kg s^-1 | Cumulative mass flow inlet minus outlet |
COOLER.P | 1101325 | m^-1 kg s^-2 | Pressure |
COOLER.T | 278,15 | K | Temperature |
COOLER.alfa | 0 | Molar vapor fraction | |
COOLER.cduty | 258413,05 | m^2 kg s^-3 | Cumulative enthalpy flow inlet minus outlet |
COOLER.cmdot | 0 | kg s^-1 | Cumulative mass flow inlet minus outlet |
COOLER.deltaP | 20000 | m^-1 kg s^-2 | Pressure drop |
COOLER.deltas | 2435,25 | m^2 kg K^-1 s^-3 | Entropy power |
COOLER.duty | 258413,05 | m^2 kg s^-3 | Duty inlet - outlet |
COOLER.flowcoefficient | 19177522932,21 | m^-7 kg | Flow coefficient |
HEATER.P | 1131628,16 | m^-1 kg s^-2 | Pressure |
HEATER.T | 363,15 | K | Temperature |
HEATER.alfa | 0 | Molar vapor fraction | |
HEATER.cduty | -262747,8 | m^2 kg s^-3 | Cumulative enthalpy flow inlet minus outlet |
HEATER.cmdot | 0 | kg s^-1 | Cumulative mass flow inlet minus outlet |
HEATER.deltaP | 10000 | m^-1 kg s^-2 | Pressure drop |
HEATER.deltas | -2260,37 | m^2 kg K^-1 s^-3 | Entropy power |
HEATER.duty | -262747,8 | m^2 kg s^-3 | Duty inlet - outlet |
HEATER.flowcoefficient | 9962933819,3 | m^-7 kg | Flow coefficient |
HOLD.At | 0 | m^2 | Cross-section |
HOLD.E | 0,5 | m^2 s^-2 | mass kinetic energy |
HOLD.P | 1131325 | m^-1 kg s^-2 | Pressure |
HOLD.Re | 111846,26 | Reynolds number | |
HOLD.T | 363,15 | K | Temperature |
HOLD.V | 0 | m^3 | Volume |
HOLD.alfa | 0 | Molar vapor fraction | |
HOLD.cduty | 0 | m^2 kg s^-3 | Cumulative enthalpy flow inlet minus outlet |
HOLD.cmdot | 0 | kg s^-1 | Cumulative mass flow inlet minus outlet |
HOLD.deltaP | 303,16 | m^-1 kg s^-2 | Pressure drop |
HOLD.deltaPfrictional | 303,16 | m^-1 kg s^-2 | Frictional pressure drop |
HOLD.deltaPgravitational | 0 | m^-1 kg s^-2 | Gravitational pressure drop |
HOLD.deltas | -0,12 | m^2 kg K^-1 s^-3 | Entropy power |
HOLD.di | 0,04 | m | Internal diameter |
HOLD.duty | 0 | m^2 kg s^-3 | Duty inlet - outlet |
HOLD.ed | 0 | Adimensional rugosity | |
HOLD.f | 0,02 | Moody friction factor | |
HOLD.flowcoefficient | 282559549,05 | m^-7 kg | Flow coefficient |
HOLD.mu | 0 | m^-1 kg s^-1 | Viscosity |
HOLD.rho | 965,43 | m^-3 kg | Density |
HOLD.tau | 1 | s | Residence time |
HOLD.theta | 0 | Angle positive for ascending | |
HOLD.v | 1 | m s^-1 | Velocity |
HOLD.vhConcentrated | 0 | velocity heads due to concentrated pressure losses | |
HOLD.vhDistributed | 0,63 | velocity heads due to distributed pressure losses | |
PUMP.P | 1141628,16 | m^-1 kg s^-2 | Pressure |
PUMP.T | 297,15 | K | Temperature |
PUMP.We | -1299,08 | m^2 kg s^-3 | Electrical power |
PUMP.Wf | -1052,26 | m^2 kg s^-3 | Fluid power |
PUMP.Wm | -1169,17 | m^2 kg s^-3 | Shaft power |
PUMP.alfa | 0 | Molar vapor fraction | |
PUMP.cduty | 0 | m^2 kg s^-3 | Cumulative enthalpy flow inlet minus outlet |
PUMP.cmdot | 0 | kg s^-1 | Cumulative mass flow inlet minus outlet |
PUMP.deltaP | -1050303,16 | m^-1 kg s^-2 | Pressure drop |
PUMP.deltas | 1165,7 | m^2 kg K^-1 s^-3 | Entropy power |
PUMP.duty | 0 | m^2 kg s^-3 | Duty inlet - outlet |
PUMP.flowcoefficient | -1045558781128,8 | m^-7 kg | Flow coefficient |
PUMP.i | -2,19 | A | Current |
PUMP.rho | 998,14 | m^-3 kg | Fluid density |
REC.A | 1,03 | m^2 | Heat transfer area |
REC.cduty | 0 | m^2 kg s^-3 | Cumulative enthalpy flow inlet minus outlet |
REC.cmdot | 0 | kg s^-1 | Cumulative mass flow inlet minus outlet |
REC.coldP | 91325 | m^-1 kg s^-2 | Pressure of cold outlet stream |
REC.coldT | 297,15 | K | Temperature of cold outlet stream |
REC.coldapproach | 66 | K | Temperature approach for cold stream |
REC.coldflowcoefficient | 10018815365,94 | m^-7 kg | Flow coefficient cold side |
REC.deltaPcold | 10000 | m^-1 kg s^-2 | Pressure difference for cold stream |
REC.deltaPhot | 10000 | m^-1 kg s^-2 | Pressure difference for hot stream |
REC.deltaTcold | 20 | K | Temperature difference for cold stream |
REC.deltaThot | -22,32 | K | Temperature difference for hot stream |
REC.dutyhot | 85462,05 | m^2 kg s^-3 | Hot side duty absolute value |
REC.heat_losses | 0 | m^2 kg s^-3 | Heat losses to environment dutyhot minus dutycold |
REC.hotP | 1121325 | m^-1 kg s^-2 | Pressure of hot outlet stream |
REC.hotT | 340,83 | K | Temperature of hot outlet stream |
REC.hotapproach | 63,68 | K | Temperature approach for hot stream |
REC.hotflowcoefficient | 9320452411,64 | m^-7 kg | Flow coefficient hot side |
S01.P | 101325 | m^-1 kg s^-2 | Pressure |
S01.T | 277,15 | K | Temperature |
S01:Tphase.fraction | 1 | phase fraction | |
S01:Tphase.mdot | 1 | kg s^-1 | mass flow |
S01:Tphase.w[0] | 1 | mass fraction of water | |
S01:Tphase.w[1] | 0 | mass fraction of prote | |
S01:Tphase.w[2] | 0 | mass fraction of lipid | |
S01:Tphase.w[3] | 0 | mass fraction of carbo | |
S01:Tphase.w[4] | 0 | mass fraction of fiber | |
S02.P | 91325 | m^-1 kg s^-2 | Pressure |
S02.T | 297,15 | K | Temperature |
S02:Tphase.fraction | 1 | phase fraction | |
S02:Tphase.mdot | 1 | kg s^-1 | mass flow |
S02:Tphase.w[0] | 1 | mass fraction of water | |
S02:Tphase.w[1] | 0 | mass fraction of prote | |
S02:Tphase.w[2] | 0 | mass fraction of lipid | |
S02:Tphase.w[3] | 0 | mass fraction of carbo | |
S02:Tphase.w[4] | 0 | mass fraction of fiber | |
S03.P | 1141628,16 | m^-1 kg s^-2 | Pressure |
S03.T | 297,15 | K | Temperature |
S03:Tphase.fraction | 1 | phase fraction | |
S03:Tphase.mdot | 1 | kg s^-1 | mass flow |
S03:Tphase.w[0] | 1 | mass fraction of water | |
S03:Tphase.w[1] | 0 | mass fraction of prote | |
S03:Tphase.w[2] | 0 | mass fraction of lipid | |
S03:Tphase.w[3] | 0 | mass fraction of carbo | |
S03:Tphase.w[4] | 0 | mass fraction of fiber | |
S04.P | 1131628,16 | m^-1 kg s^-2 | Pressure |
S04.T | 363,15 | K | Temperature |
S04:Tphase.fraction | 1 | phase fraction | |
S04:Tphase.mdot | 1 | kg s^-1 | mass flow |
S04:Tphase.w[0] | 1 | mass fraction of water | |
S04:Tphase.w[1] | 0 | mass fraction of prote | |
S04:Tphase.w[2] | 0 | mass fraction of lipid | |
S04:Tphase.w[3] | 0 | mass fraction of carbo | |
S04:Tphase.w[4] | 0 | mass fraction of fiber | |
S05.P | 1131325 | m^-1 kg s^-2 | Pressure |
S05.T | 363,15 | K | Temperature |
S05:Tphase.fraction | 1 | phase fraction | |
S05:Tphase.mdot | 1 | kg s^-1 | mass flow |
S05:Tphase.w[0] | 1 | mass fraction of water | |
S05:Tphase.w[1] | 0 | mass fraction of prote | |
S05:Tphase.w[2] | 0 | mass fraction of lipid | |
S05:Tphase.w[3] | 0 | mass fraction of carbo | |
S05:Tphase.w[4] | 0 | mass fraction of fiber | |
S05bis.P | 1131325,04 | m^-1 kg s^-2 | Pressure |
S05bis.T | 363,15 | K | Temperature |
S05bis:Tphase.fraction | 1 | phase fraction | |
S05bis:Tphase.mdot | 1 | kg s^-1 | mass flow |
S05bis:Tphase.w[0] | 1 | mass fraction of water | |
S05bis:Tphase.w[1] | 0 | mass fraction of prote | |
S05bis:Tphase.w[2] | 0 | mass fraction of lipid | |
S05bis:Tphase.w[3] | 0 | mass fraction of carbo | |
S05bis:Tphase.w[4] | 0 | mass fraction of fiber | |
S06.P | 1121325 | m^-1 kg s^-2 | Pressure |
S06.T | 340,83 | K | Temperature |
S06:Tphase.fraction | 1 | phase fraction | |
S06:Tphase.mdot | 1 | kg s^-1 | mass flow |
S06:Tphase.w[0] | 1 | mass fraction of water | |
S06:Tphase.w[1] | 0 | mass fraction of prote | |
S06:Tphase.w[2] | 0 | mass fraction of lipid | |
S06:Tphase.w[3] | 0 | mass fraction of carbo | |
S06:Tphase.w[4] | 0 | mass fraction of fiber | |
S07.P | 1101325 | m^-1 kg s^-2 | Pressure |
S07.T | 278,15 | K | Temperature |
S07:Tphase.fraction | 1 | phase fraction | |
S07:Tphase.mdot | 1 | kg s^-1 | mass flow |
S07:Tphase.w[0] | 1 | mass fraction of water | |
S07:Tphase.w[1] | 0 | mass fraction of prote | |
S07:Tphase.w[2] | 0 | mass fraction of lipid | |
S07:Tphase.w[3] | 0 | mass fraction of carbo | |
S07:Tphase.w[4] | 0 | mass fraction of fiber | |
sink.cduty | -15954669,04 | m^2 kg s^-3 | Cumulative enthalpy flow inlet minus outlet |
sink.cmdot | 1 | kg s^-1 | Cumulative mass flow inlet minus outlet |
source.cduty | 15959003,8 | m^2 kg s^-3 | Cumulative enthalpy flow inlet minus outlet |
source.cmdot | -1 | kg s^-1 | Cumulative mass flow inlet minus outlet |
Stream table results:
S01 - Fluid inlet | S02 - Pre-heated fluid | S03 - Pumped pre-heated fluid | S04 - Holding hot fluid | S05 - Pasteurized fluid | S06 - Warm fluid | S07 - Cooled fluid outlet | S05bis - Pasteurized fluid cut | |
---|---|---|---|---|---|---|---|---|
Pressure, barg | 0.000 | -0.100 | 10.448 | 10.348 | 10.300 | 10.200 | 10.000 | 10.300 |
Temperature, °C | 4.0 | 24.0 | 24.0 | 83.0 | 83.0 | 61.1 | 5.0 | 83.0 |
V, m3/h | 3.513 | 3.526 | 3.525 | 3.624 | 3.624 | 3.579 | 3.512 | 3.624 |
M, kg/h | 3600.0 | 3600.0 | 3600.0 | 3600.0 | 3600.0 | 3600.0 | 3600.0 | 3600.0 |
N, kmol/h | 199.83 | 199.83 | 199.83 | 199.83 | 199.83 | 199.83 | 199.83 | 199.83 |
M[water], kg/h | 3194.1 | 3194.1 | 3194.1 | 3194.1 | 3194.1 | 3194.1 | 3194.1 | 3194.1 |
M[protein], kg/h | 114.2 | 114.2 | 114.2 | 114.2 | 114.2 | 114.2 | 114.2 | 114.2 |
M[lipid], kg/h | 117.8 | 117.8 | 117.8 | 117.8 | 117.8 | 117.8 | 117.8 | 117.8 |
M[carbohydrate], kg/h | 174.0 | 174.0 | 174.0 | 174.0 | 174.0 | 174.0 | 174.0 | 174.0 |
M[fiber], kg/h | 0.0 | 0.0 | 0.0 | 0.0 | 0.0 | 0.0 | 0.0 | 0.0 |
w[water] | 88.72% | 88.72% | 88.72% | 88.72% | 88.72% | 88.72% | 88.72% | 88.72% |
w[protein] | 3.17% | 3.17% | 3.17% | 3.17% | 3.17% | 3.17% | 3.17% | 3.17% |
w[lipid] | 3.27% | 3.27% | 3.27% | 3.27% | 3.27% | 3.27% | 3.27% | 3.27% |
w[carbohydrate] | 4.83% | 4.83% | 4.83% | 4.83% | 4.83% | 4.83% | 4.83% | 4.83% |
w[fiber] | 0.00% | 0.00% | 0.00% | 0.00% | 0.00% | 0.00% | 0.00% | 0.00% |